Das französische Solarenergieinstitut Ines hat neue PV -Module mit Thermoplastik und Naturfasern in Europa wie Flachs und Basalt entwickelt. Die Wissenschaftler wollen den ökologischen Fußabdruck und das Gewicht von Sonnenkollektoren reduzieren und gleichzeitig das Recycling verbessern.
Eine recycelte Glasplatte vorne und ein Leinenverbund auf der Rückseite
Bild: GD
Aus dem PV -Magazin Frankreich
Forscher des Frankreichs National Solar Energy Institute (INES)-eine Aufteilung der französischen alternativen Energien und Atomergie-Kommission (CEA)-entwickeln Solarmodule mit neuen biologischen Materialien auf der vorderen und hinteren Seite.
„Da der CO2-Fußabdruck und die Lebenszyklusanalyse inzwischen zu wesentlichen Kriterien für die Auswahl von Photovoltaik-Panels geworden sind, wird die Beschaffung von Materialien in den nächsten Jahren zu einem entscheidenden Element in Europa“, sagte Anis Fouini, Direktor von CEA-Inses in einem Interview mit dem PV -Magazin Frankreich.
Aude Derrier, die Koordinatorin des Forschungsprojekts, sagte, ihre Kollegen hätten sich die verschiedenen bereits existierenden Materialien angesehen, um einen zu finden, mit dem Modulhersteller Panels herstellen können, die die Leistung, Haltbarkeit und Kosten verbessern und gleichzeitig die Umweltauswirkungen senken. Der erste Demonstrator besteht aus Heterojunction (HTJ) -Solarzellen, die in ein All-Composite-Material integriert sind.
"Die Vorderseite besteht aus einem mit Glasfaser gefüllten Polymer, das Transparenz liefert", sagte Derrier. "Die hintere Seite besteht aus Verbundwerkstoffen, die auf Thermoplastik basieren, in der ein Weben von zwei Fasern, Flachs und Basalt, integriert wurde, was mechanische Festigkeit, aber auch einen besseren Widerstand gegen Feuchtigkeit liefert."
Der Flachs stammt aus Nordfrankreich, wo das gesamte industrielle Ökosystem bereits vorhanden ist. Der Basalt wird anderswo in Europa bezogen und von einem Industriepartner von INES gewebt. Dies reduzierte den CO2 -Fußabdruck um 75 Gramm CO2 pro Watt im Vergleich zu einem Referenzmodul derselben Leistung. Das Gewicht wurde ebenfalls optimiert und beträgt weniger als 5 Kilogramm pro Quadratmeter.
"Dieses Modul richtet sich an den PV auf dem Dach und die Integration des Gebäudes", sagte Derrier. „Der Vorteil ist, dass es natürlich schwarz ist, ohne dass ein Rückblatt erforderlich ist. In Bezug auf das Recycling ist die Trennung der Schichten auch technisch einfacher, dank der Thermoplastik, die wiedergegeben werden kann. “
Das Modul kann ohne Anpassung aktueller Prozesse erfolgen. Laut Derrier sei die Idee, die Technologie ohne zusätzliche Investitionen auf Hersteller zu übertragen.
"Das einzige Notwendigkeit ist es, Gefriergeräte zu haben, um das Material zu speichern und den Vernetzungsprozess des Harzes zu starten, aber die meisten Hersteller verwenden heute Prepreg und sind bereits dafür gerüstet", sagte sie.
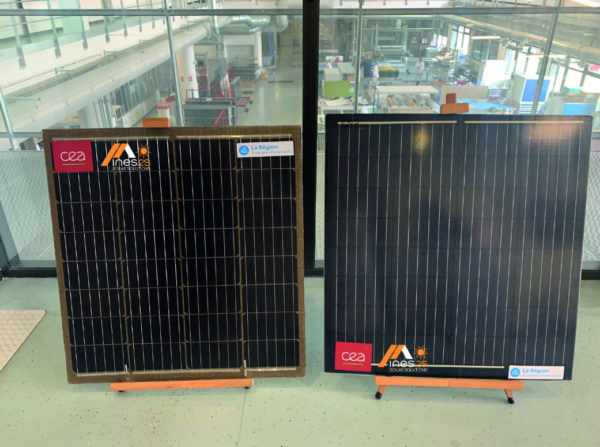
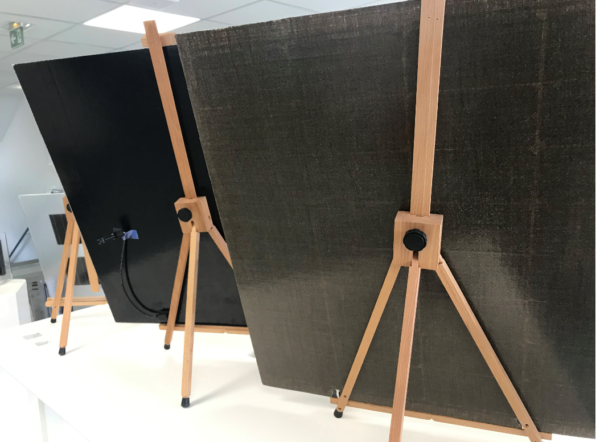
„Wir haben an der zweiten Lebensdauer von Glas gearbeitet und ein Modul entwickelt, das aus wiederverwendetem 2,8 -mm -Glas besteht, das aus einem alten Modul stammt“, sagte Derrier. "Wir haben auch ein thermoplastisches Einkapsel verwendet, das keine Vernetzung erfordert, die daher leicht zu recyceln ist, und ein thermoplastisches Verbund mit Flachsfasern zur Resistenz."
Die basaltfreie hintere Seite des Moduls hat eine natürliche Leinenfarbe, die beispielsweise für Architekten ästhetisch interessant sein könnte. Darüber hinaus zeigte das INES -Berechnungswerkzeug eine Verringerung des CO2 -Fußabdrucks um 10%.
"Es ist jetzt unerlässlich, die Photovoltaik -Versorgungsketten in Frage zu stellen", sagte Jouini. „Mit Hilfe der Rhône-Alpes-Region im Rahmen des internationalen Entwicklungsplans suchten wir daher nach Spielern außerhalb des Solarsektors, um neue Thermoplastik und neue Fasern zu finden. Wir haben auch über den aktuellen Laminierungsprozess nachgedacht, der sehr energieintensiv ist. “
Zwischen dem Druck, der Presse und der Kühlphase dauert die Lamination normalerweise zwischen 30 und 35 Minuten, wobei eine Betriebstemperatur von etwa 150 ° C bis 160 ° C.
"Bei Modulen, die zunehmend um Öko-gestaltete Materialien enthalten, müssen die Thermoplastik auf etwa 200 ° C bis 250 ° C transformiert werden, da die HTJ-Technologie auf Wärme empfindlich ist und 200 ° C nicht überschreiten darf", sagte Derrier.
Das Research Institute arbeitet mit dem Frankreich-basierten Induktionsthermokompressionspezialisten Roctool zusammen, um die Zykluszeiten zu verkürzen und Formen entsprechend den Bedürfnissen der Kunden herzustellen. Zusammen haben sie ein Modul mit einer hinteren Gesichtsfläche aus thermoplastischem Verbundwerkstoffe vom Typ polypropylen entwickelt, zu dem recycelte Kohlenstofffasern integriert wurden. Die Vorderseite besteht aus Thermoplastik und Glasfaser.
"Roctools Induktionsthermokompressionsprozess ermöglicht es, die beiden vorderen und hinteren Platten schnell zu erhitzen, ohne 200 ° C im Kern der HTJ -Zellen erreichen zu müssen", sagte Derrier.
Das Unternehmen behauptet, die Investition sei niedriger und der Prozess könnte eine Zykluszeit von nur wenigen Minuten erreichen, während sie weniger Energie nutzen. Die Technologie richtet sich an Verbundhersteller, um ihnen die Möglichkeit zu geben, Teile unterschiedlicher Formen und Größen zu erzeugen und gleichzeitig leichtere und haltbarere Materialien zu integrieren.
Postzeit: Jun-24. Juni 2022